Top Uses and Benefits of Automated Guided Vehicles (AGVs)
- Christian Alsop
- Jan 23
- 10 min read
Updated: Jan 29
Automated Guided Vehicles (AGVs) are self-guided vehicles that automate material handling in manufacturing, warehouses, and distribution centers. They enhance efficiency and safety while reducing manual labor. This article explores the key applications, types, and advantages of AGVs.
Key Takeaways
Automated Guided Vehicles (AGVs) enhance efficiency in manufacturing and logistics by automating material transport, reducing manual labor, and optimizing operations.
AGVs come in various types, including Automated Guided Carts, Forklift AGVs, and Towing AGVs, each tailored to specific material handling needs.
While AGVs offer significant productivity gains and improved space utilization, challenges like high initial investment and integration complexities must be carefully managed.
Key Applications of Automated Guided Vehicles (AGVs)

Automated Guided Vehicles (AGVs) are revolutionizing manufacturing facilities, warehouses, and distribution centers by automating tasks traditionally handled by humans or fixed conveyor systems. These self-guided vehicles enhance safety and productivity, reduce manual labor, and offer unparalleled flexibility in material handling operations, including the use of automatic guided vehicle technology and autonomous guided vehicles.
From transporting raw materials to handling finished goods, raw materials agvs are becoming the backbone of efficient and modern supply chains.
Transporting Raw Materials
In manufacturing facilities, the efficient transport of raw materials is crucial for maintaining a steady production flow in the manufacturing facility.
AGVs are increasingly replacing traditional conveyor systems, offering more flexibility and reliability in an agv system.
These automated vehicles can transport various raw materials, including:
metal
chemicals
plastic
paper
This ensures that production lines never run out of essential components.
Tugger AGVs, for instance, can tow multiple trailers or carts simultaneously, making them ideal for transporting bulk loads within a facility.
The implementation of Automated Guided Carts (AGCs) further enhances material handling by efficiently transporting small items and waste within storage locations. Automating the movement of raw materials with AGVs reduces reliance on manual labor, minimizes human error, and streamlines distribution center operations.
Work-in-Process Movement
AGVs play a pivotal role in optimizing the movement of partially completed goods along production lines. These vehicles facilitate the smooth transfer of materials between different stages of the manufacturing process, ensuring a seamless workflow and minimizing delays. Automating the transport of work-in-process items with AGVs helps maintain a consistent production pace, meeting deadlines and maximizing productivity.
The use of AGVs in work-in-process movement reduces the need for manual labor, allowing human operators to focus on more complex tasks. This automation not only enhances operational efficiency but also leads to significant improvements in overall productivity and workflow optimization within manufacturing facilities.
Handling Finished Goods
Once products are completed, they need to be efficiently moved to storage or shipping areas. AGVs are instrumental in handling finished goods, reducing the risk of damage during transport and ensuring that products reach their destinations safely. Heavy burden carriers, equipped with self-loading capabilities, are specifically designed to transport substantial loads safely and efficiently, minimizing damage costs and improving labor efficiencies.
Automating the movement of finished goods with AGVs streamlines the manufacturing process and enhances overall operational efficiency. The ability to handle large volumes of products without human intervention not only reduces the risk of errors but also speeds up the entire logistics chain, from production to delivery.
Warehouse Operations
In warehouse operations, AGVs offer unparalleled flexibility and efficiency. These automated vehicles manage tasks such as stock replenishment and order picking, providing greater flexibility compared to fixed conveyor systems. AGVs can navigate tight spaces and streamline operations, making the most of available storage areas and optimizing warehouse layouts.
The compact design of AGVs allows for better space utilization, freeing up areas for additional storage or other operational needs. Furthermore, collaborative mobile robots can work alongside AGVs, increasing efficiency in picking tasks without taking up extra space, thus enhancing overall productivity and operational effectiveness in distribution centers.
Types of Automated Guided Vehicles

AGVs come in various types, each designed to cater to specific material handling needs and operational environments. From Automated Guided Carts (AGCs) to Forklift AGVs, Unit Load AGVs, Towing AGVs, Heavy Burden Carriers, and Hybrid AGVs, these vehicles offer a wide range of capabilities to meet the diverse demands of modern manufacturing and logistics operations.
Automated Guided Carts (AGCs)
Automated Guided Carts (AGCs) are the simplest form of AGVs, designed to follow predefined paths and transport smaller loads such as components, tools, waste, and equipment within facilities. These AGVs excel in environments where flexibility and efficiency are paramount, offering a cost-effective solution for automating material handling tasks.
Forklift AGVs
Forklift AGVs are a common sight in warehouses and manufacturing facilities, where they perform tasks such as lifting, stacking, loading, and unloading items from racks and trucks. By automating these functions, forklift AGVs significantly increase operational efficiency and reduce the risk of injuries associated with manual forklift operations.
Unit Load AGVs
Unit Load AGVs are designed to transport individual unit loads like pallets, containers, or racks, making them essential for moving various items within a facility. These AGVs handle tasks such as pallet movement, loading/unloading, and storage, ensuring efficient and reliable material handling operations.
Towing AGVs (Tuggers)
Towing AGVs, also known as tuggers, operate autonomously. Their primary function is to pull or tow carts and trailers. Equipped with a hitch mechanism, these AGVs can connect and transport multiple loads simultaneously, making them ideal for bulk material handling tasks.
Their low profile and small chassis allow them to engage carts or shelves underneath, enhancing their versatility and efficiency.
Heavy Burden Carriers
Heavy burden carriers are specifically designed to transport heavy loads within facilities. These AGVs come equipped with self-loading capabilities and advanced steering options, making them suitable for handling substantial material handling tasks efficiently and safely.
Hybrid AGVs
Hybrid AGVs combine autonomous operation with manual control, offering flexibility for diverse material handling tasks. These vehicles can operate autonomously for routine tasks and switch to manual control when required, providing a versatile solution for dynamic operational environments.
How Automated Guided Vehicles Work

Automated Guided Vehicles (AGVs) operate by following defined paths using various guidance technologies like magnetic tape, laser navigation, and optical systems. Equipped with advanced sensors, these automated guided vehicle navigate safely and efficiently within warehouses, ensuring precise and reliable material handling operations.
Navigation Systems
AGVs employ various navigation methods to ensure accurate and efficient operation. Laser-guided AGVs use a laser positioning system to determine their location by reflecting signals off predetermined targets, providing precise navigation. Magnetic tape navigation, another common method, involves sensors on AGVs following a path created by magnetic tape installed on the floor, ensuring a fixed path for the vehicle.
Inertial navigation systems use gyroscopes and accelerometers to track AGV movements from a known starting point, while outdoor operations may utilize GPS for navigation, though this is less common indoors due to satellite signal limitations. Line following and advanced natural navigation techniques are also employed by AGCs, enhancing their flexibility and operational efficiency.
Steering Control
Steering control is a critical aspect of AGV operation, ensuring precise directional movements. Differential speed control is a common method, where varying the speeds of two drive wheels allows the AGV to change direction. This technique is essential for navigating tight spaces and maintaining accurate paths within operational environments.
Steered wheel control is another method used by AGVs to achieve precise directional movements, involving additional steering motors for enhanced maneuverability. These steering techniques are vital for the accurate navigation of AGVs, ensuring reliable and efficient material handling operations.
Traffic Management
Effective traffic management strategies are crucial for the safe and efficient operation of multiple AGVs within a facility. Zone control sensors are a common strategy, where specific areas are assigned for AGV operations to minimize the risk of collisions. This approach helps manage the movement of multiple AGVs, ensuring smooth and coordinated operations.
Lidar and ultrasonic sensors on AGVs detect obstacles and initiate safety measures to prevent collisions. Collision avoidance sensors play a vital role in ensuring the safety of AGV operations, reducing the risk of accidents and enhancing overall operational efficiency.
Advantages and Challenges of Implementing AGVs
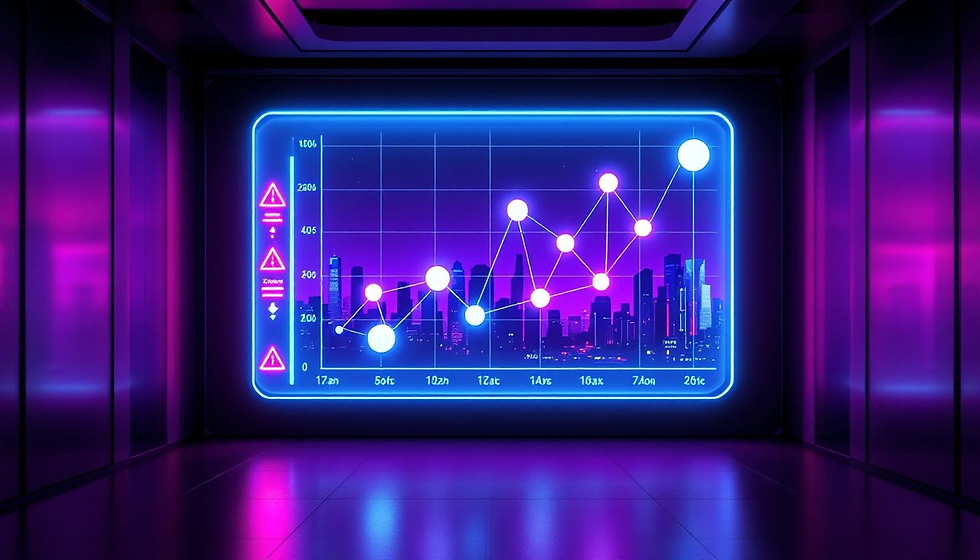
Implementing AGVs offers numerous advantages, such as increased efficiency, enhanced safety, and reduced labor costs. However, challenges like high initial investment and compatibility with existing systems can pose significant hurdles.
Understanding these pros and cons is essential for businesses considering AGV adoption.
Increased Efficiency and Productivity
The use of AGVs dramatically enhances efficiency and productivity within manufacturing facilities. AGVs ensure a reliable and steady supply of raw materials to production lines, eliminating human intervention and reducing errors. This automation leads to significant improvements in operational efficiency and productivity, allowing human workers to focus on more complex and value-added tasks.
AGVs also contribute to overall operational efficiency by reducing manual labor requirements and minimizing human errors in warehouses and manufacturing environments. This results in a smoother workflow and higher productivity, making AGVs a valuable asset for modern industrial operations.
Cost Considerations
While the initial investment for AGVs can be substantial, posing a challenge for smaller companies, the long-term cost benefits often justify the expense. AGVs generally offer lower operational costs over time, resulting in significant labor savings and reduced risk of injuries and associated expenses. Many businesses find that the return on investment for AGVs can be realized within one to two years, making them a financially viable option in the long run.
However, for smaller operations with straightforward and fixed transport needs, traditional conveyor systems may be more cost-effective. Integrating AGVs with Warehouse Management Systems (WMS) can also help reduce labor costs associated with manual handling, further enhancing the financial benefits of AGV implementation.
Space Utilization
AGVs play a crucial role in enhancing space utilization within manufacturing facilities and warehouses. Their compact design and advanced navigation capabilities allow them to operate efficiently in tight spaces, making better use of the available area. Reducing the need for wide aisles and enabling flexible layout planning, AGVs optimize storage locations and improve space management.
Moreover, AGVs’ ability to transport substantial loads within limited space makes them a superior choice compared to overhead trolleys, which may save floor space but lack the mobility and operational flexibility of AGVs. This enhanced space utilization translates into increased storage capacity and improved operational efficiency.
Implementation Challenges
Implementing AGVs comes with its own set of challenges, including the need for infrastructure modifications and ensuring compatibility with existing systems. Safety concerns and the complexity of integrating AGVs into current operations can also pose significant hurdles. Proper planning and a thorough understanding of the facility’s layout and requirements are essential to overcoming these challenges.
Additionally, training employees on AGV operation and maintenance is crucial for a smooth transition. Addressing these challenges proactively can help businesses leverage the full potential of AGVs while minimizing disruptions during the implementation phase.
Alternatives to Automated Guided Vehicles
While AGVs offer numerous benefits, there are several alternatives that businesses can consider for their material handling needs. Each alternative provides unique advantages and can be more suitable depending on the specific requirements of the operation.
Understanding these options helps companies make informed decisions about the best technology to implement.
Conveyor Systems
Conveyor systems are a traditional alternative to AGVs, offering a fixed path for continuous material flow. Unlike the mobility and route flexibility provided by AGVs, conveyor systems are stationary installations designed for continuous operation. They are cost-effective for straightforward transport needs but lack the adaptability and flexibility of AGVs in dynamic environments.
Automated Storage and Retrieval Systems (AS/RS)
Automated Storage and Retrieval Systems (AS/RS) offer significant advantages in terms of transportation and storage capabilities, providing ultra-dense storage capacity and freeing up to 400% more space. These systems are particularly beneficial for operations requiring high storage density and efficiency. However, they require inventory to be stored in bins or totes that are tightly stacked, which can be a limitation for handling larger items.
AGVs can complement AS/RS by automating the material handling of items that are not suitable for grid storage, enhancing the overall efficiency of storage and retrieval operations. Integrating AGVs with AS/RS frameworks can significantly improve buffer storage, staging orders for shipping, and implementing get-to-person strategies.
Autonomous Mobile Robots (AMRs)
Autonomous mobile robots (AMRs) are another alternative to AGVs, offering greater flexibility and adaptability in dynamic environments. Unlike AGVs, which follow predefined paths, an autonomous mobile robot navigates dynamically using sensors and cameras, making them more suitable for environments where the layout frequently changes. This flexibility allows AMRs to operate efficiently in complex and unpredictable settings.
The main consideration when choosing between AGVs and AMRs is the predictability of the operational environment versus the need for flexibility. While AGVs excel in stable environments with consistent paths, AMRs are ideal for dynamic operations where adaptability is crucial.
Overhead Trolleys
Overhead trolleys serve as an effective alternative to AGVs in various material handling operations, particularly in environments where vertical space optimization is essential. These systems minimize the footprint on the facility floor by utilizing vertical space efficiently.
However, their mobility and operational flexibility are generally more limited compared to AGVs, making them less suitable for dynamic and complex material handling tasks.
Integration of AGVs with Other Systems
Integrating AGVs with other systems, such as Warehouse Management Systems (WMS) and Enterprise Resource Planning (ERP) systems, significantly enhances material handling efficiency. This integration provides better visibility into material locations and quantities, streamlining operations and reducing manual handling tasks.
Enhancing Warehouse Operations
Connecting AGVs to WMS or ERP systems allows for automatic updates on inventory status as materials are relocated, reducing manual handling tasks and improving operational efficiency. This integration ensures that inventory records are always up-to-date, enabling more accurate and efficient warehouse management.
However, integrating AGVs with existing systems can present challenges, such as ensuring compatibility and making necessary infrastructure modifications. Overcoming these challenges requires careful planning and a thorough understanding of the facility’s needs and capabilities.
Collaborative Mobile Robots
Collaborative mobile robots work alongside AGVs to enhance picking operations and other material handling tasks. These robots are designed to assist the human operator, increasing efficiency and productivity without requiring additional space.
Integrating collaborative mobile robots with AGVs creates a more flexible and efficient material handling system, leveraging the strengths of both technologies.
Summary
Automated Guided Vehicles (AGVs) are transforming the landscape of material handling in manufacturing facilities, warehouses, and distribution centers. These advanced vehicles offer unparalleled efficiency, safety, and flexibility, making them indispensable in modern industrial operations. From transporting raw materials to handling finished goods, AGVs optimize every stage of the supply chain, enhancing productivity and reducing labor costs.
While implementing AGVs comes with its own set of challenges, the long-term benefits often outweigh the initial hurdles. By understanding the different types of AGVs, their operational mechanisms, and the integration possibilities with other systems, businesses can make informed decisions to enhance their material handling processes. Whether opting for AGVs or exploring alternatives like conveyor systems, AS/RS, or AMRs, the goal remains the same: to achieve greater efficiency, safety, and productivity in industrial operations.
Frequently Asked Questions
What are Automated Guided Vehicles (AGVs)?
Automated Guided Vehicles (AGVs) are self-guided vehicles employed in manufacturing and logistics to automate material handling, thereby improving efficiency and minimizing the need for manual labor.
How do AGVs navigate within a facility?
AGVs navigate within a facility by employing navigation methods such as laser-guided systems, magnetic tape, and inertial navigation, ensuring safe and efficient movement along predetermined paths.
What are the main benefits of using AGVs?
The main benefits of using AGVs include increased efficiency, enhanced safety, reduced labor costs, and improved space utilization, all of which result from their ability to automate repetitive tasks and optimize material handling operations. This automation minimizes human error, making processes more reliable.
What are some challenges associated with implementing AGVs?
Implementing Autonomous Guided Vehicles (AGVs) presents challenges such as significant initial investment, necessary modifications to existing infrastructure, compatibility with current systems, and the requirement for thorough employee training on operation and maintenance. Addressing these issues is crucial for successful integration.
How do AGVs integrate with other systems in a warehouse?
AGVs integrate with Warehouse Management Systems (WMS) and Enterprise Resource Planning (ERP) systems to improve visibility and streamline warehouse operations. This integration enhances efficiency in managing material locations and quantities.
Comentários